Optimizing the sealing structure can significantly reduce gas leakage between various components inside the blower. Gas leakage not only leads to pressure loss but also decreases the efficiency of the blower. By enhancing sealing performance, it ensures effective compression and transmission of gas inside the blower, thereby improving overall performance.
Multistage centrifugal blowers are typically used in situations requiring high pressure. Optimizing the sealing structure enhances the blower's stability under high pressure, preventing pressure drop due to leakage. This helps meet specific pressure requirements in application scenarios and ensures the system operates normally.
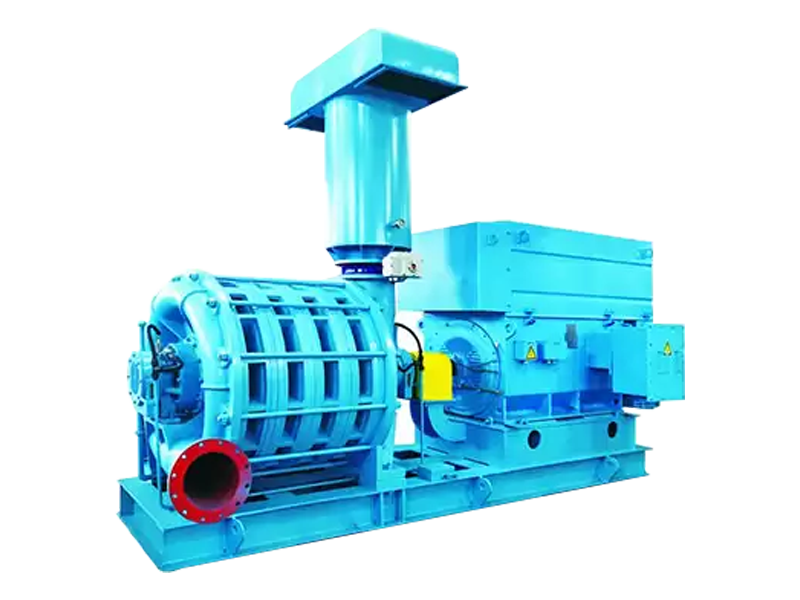
A good sealing structure reduces the entry of impurities and particles into the blower, thereby reducing wear and corrosion of internal components. This helps extend the blower's lifespan and reduces the frequency of maintenance and part replacements.
Optimizing the sealing structure can reduce system fluctuations and instability caused by leakage. Stable blower operation contributes to ensuring the stability and reliability of the entire system, reducing the risk of failures.
Optimizing the internal sealing structure of Multistage centrifugal blowers plays a significant role in reducing gas leakage, enhancing pressure retention capability, reducing energy consumption, prolonging equipment lifespan, and improving system stability.